1.5" Lower in 1 hour
#1
1.5" Lower in 1 hour
I like my 6MT suspension. Ride quality and handling are excellent. Only think I don’t like about it is ride height. So I decided to lower it for 1.5”, but I didn’t want to ride on my bump stoppers with just springs, or to spend a ton of money for coilovers. So I used my CNC machine and some aluminum leftovers and here it is. Best part is that I needed less than an hour to install custom made parts, using just basics tools. It is reversible to. In less than hour it would be stock again. Now I am working on the rears. It will be done soon.
Before
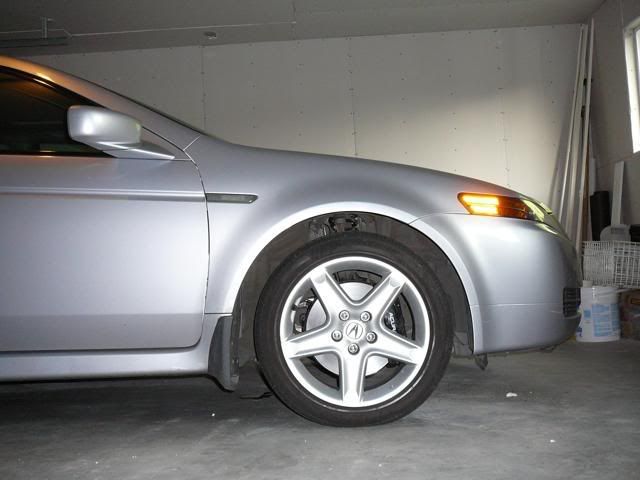
After one hour
Before
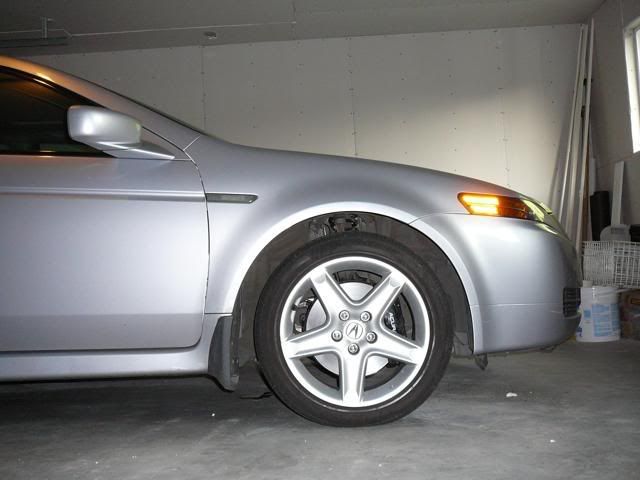
After one hour
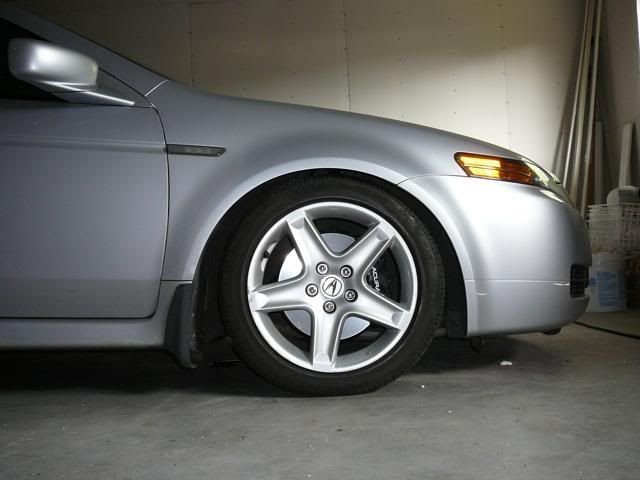
#3
Originally Posted by 01tl4tl
thats awesome looking- let us know how it rides!

Well, it rides exactly as before, except some better handling due to more negative chamber and lower center of gravity. It will be even better when the back goes down. The main idea is to make it simple, inexpensive and preserve a ride quality. I heard that many guys with A-spec suspension are happy with it, except height. It seems to me that this is the way.
#5
Originally Posted by chill_dog
It looks good. What exactly did you do? You're right about what those of us with ASPEC think...it would be pretty cool if we could duplicate this.
Trending Topics
#10
Originally Posted by I hate cars
If you ever sell whatever it is you did I will be the first in line. The rear sags due to the subs. Just want to bring the front down 1" to match the rear.

#14
Originally Posted by I hate cars
Yes!

#15
Originally Posted by mishar
OK. I am trying to perfect technology so it would be as low priced as possible. First prototype was CNC machined and that can be a bit expensive. Since you are first in a row for prototype you will be first to know when it is ready. 


#16
Originally Posted by chill_dog
Three people have asked, but you've ignored it, so I'm guessing you're not going to tell us exactly what you're doing?
#17
Originally Posted by KSuchdeve
What are you actually doing here and can it be done to a 2G TL?
I'd like a decent drop but don't want to shell out for coilovers just yet.
I'd like a decent drop but don't want to shell out for coilovers just yet.
#18
Originally Posted by I hate cars
I used to work for Top CNC here in Bakersfield. You could just send me the program. 


#21

He made a set of shorter 12/13s. These forks connect the strut to the lower control arm member.
Interesting approach, but this is a very BAD move in the front. Your driveaxle goes through that fork. As your supension travels "moves up and down", the driveshaft move with it. You have now restricted the travel at the shaft. First big bump you hit is gonna bend/break either the fork or the driveshaft...
Good luck with that. Id' take those off tonigh. I wanna see pics of your axle clearance with these installed.
Originally Posted by rondog
please don't tell me you made spring clamps...
#22
Originally Posted by chill_dog
Interesting. Looking forward to more info. As for casting, I would imagine the stock forks are cast, no?
#23
Originally Posted by Kennedy

He made a set of shorter 12/13s. These forks connect the strut to the lower control arm member.
Interesting approach, but this is a very BAD move in the front. Your driveaxle goes through that fork. As your supension travels "moves up and down", the driveshaft move with it. You have now restricted the travel at the shaft. First big bump you hit is gonna bend/break either the fork or the driveshaft...
Good luck with that. Id' take those off tonigh. I wanna see pics of your axle clearance with these installed.

#24
Not exatly, the axle pivots at the CV joint, the engine side is fixed. The axle levers up and down...
But hey, if you've tested it at full travel, I guess it's OK. Not sure I'd trust aluminum to replace such a critical suspension part, beefed up or not.
You need to be careful "selling these". The liability implications are pretty high.
But hey, if you've tested it at full travel, I guess it's OK. Not sure I'd trust aluminum to replace such a critical suspension part, beefed up or not.
You need to be careful "selling these". The liability implications are pretty high.
Originally Posted by mishar
You are right about 12/13 parts, but not about restricted travel. As a matter of fact all those parts are traveling together, and only relative travel between axle and fork comes from engine movement and it is minimal that close to the wheel. 

#26
Originally Posted by Kennedy
Not exatly, the axle pivots at the CV joint, the engine side is fixed. The axle levers up and down...
But hey, if you've tested it at full travel, I guess it's OK. Not sure I'd trust aluminum to replace such a critical suspension part, beefed up or not.
You need to be careful "selling these". The liability implications are pretty high.
But hey, if you've tested it at full travel, I guess it's OK. Not sure I'd trust aluminum to replace such a critical suspension part, beefed up or not.
You need to be careful "selling these". The liability implications are pretty high.
Aluminum is good for connecting rods on top fuel dragsters and deserves a bit more of respect.

I’ll leave to my lower to think about liability.
#28
Originally Posted by mishar
Yes, there is a very small relative travel caused by axle angle change, but the gap is smallest when you lift your car and it was tested.
Aluminum is good for connecting rods on top fuel dragsters and deserves a bit more of respect.
I’ll leave to my lower to think about liability.
Aluminum is good for connecting rods on top fuel dragsters and deserves a bit more of respect.

I’ll leave to my lower to think about liability.
... and from an ethics perspecitve, you know how this place is. These kids will snap up a $50 mod like this irregardless of the safety implications. Your decision to sell distribute a CNC design may be well intended, but could have catastrophic consequences.
Guys be careful here...
#29
Originally Posted by Kennedy
Do what ya want pal, but connecting rods are not stressed/strained in the same way as this fork.
... and from an ethics perspecitve, you know how this place is. These kids will snap up a $50 mod like this irregardless of the safety implications. Your decision to sell distribute a CNC design may be well intended, but could have catastrophic consequences.
Guys be careful here...
... and from an ethics perspecitve, you know how this place is. These kids will snap up a $50 mod like this irregardless of the safety implications. Your decision to sell distribute a CNC design may be well intended, but could have catastrophic consequences.
Guys be careful here...
It is nice that you care about ethics and “kids” welfare. Somebody has to in this wild world. But don’t sell them anything that’s not yours. Especially something that is not for sale. At least not for a while and probably not here. This thread is about development. I thought it may be interesting to follow it from the beginning for “kids” so technically inclined and so much in loved with their cars. I know it would be for me.
#30
Fair enough...
I have a Mech Eng. BE degree... so I know your language, but have never applied it outside my own wrenching and "pleasure reading"... It seems the USMC had other plans (IT/Comm) for this 20 lb head.
Although I diasagree about connecting rods and forces exerted, I can see what your trying to say... Although the fork itself predominantly deals with forces in the vertical, it also deals with a lot of torsional and lateral force (engine rock, hitting a hard bump while turning etc.), which is my view of the difference.
Certainly material selection, dynamic loads and cycling, hell even corrosion should all be considerations... Given the simplicity of the design, that's a prime candidate for a completely "overengineered" solution.
Good luck, I look forward to your progress.
From a more practical perspective,
Are you concerned about bottoming out? The stock suspension is a bit soft and underdamped to be riding that low... Perhaps some spring reenforcements should be included...?
Anyway, glad to hear you are where you are. There's nothing more dang
I have a Mech Eng. BE degree... so I know your language, but have never applied it outside my own wrenching and "pleasure reading"... It seems the USMC had other plans (IT/Comm) for this 20 lb head.
Although I diasagree about connecting rods and forces exerted, I can see what your trying to say... Although the fork itself predominantly deals with forces in the vertical, it also deals with a lot of torsional and lateral force (engine rock, hitting a hard bump while turning etc.), which is my view of the difference.
Certainly material selection, dynamic loads and cycling, hell even corrosion should all be considerations... Given the simplicity of the design, that's a prime candidate for a completely "overengineered" solution.
Good luck, I look forward to your progress.
From a more practical perspective,
Are you concerned about bottoming out? The stock suspension is a bit soft and underdamped to be riding that low... Perhaps some spring reenforcements should be included...?
Anyway, glad to hear you are where you are. There's nothing more dang
Originally Posted by mishar
As a matter of fact connecting rods and forks are stressed in a very similar way, only forces stressing connecting rods are about 100 times bigger and their changes way more frequent. But comparison of those two was just to say something about aluminium strength, definitely not a method of design. I don’t know how much do you know about dynamics, forces, stresses and materials, but I can assure you that I know what I am doing.
It is nice that you care about ethics and “kids” welfare. Somebody has to in this wild world. But don’t sell them anything that’s not yours. Especially something that is not for sale. At least not for a while and probably not here. This thread is about development. I thought it may be interesting to follow it from the beginning for “kids” so technically inclined and so much in loved with their cars. I know it would be for me.
It is nice that you care about ethics and “kids” welfare. Somebody has to in this wild world. But don’t sell them anything that’s not yours. Especially something that is not for sale. At least not for a while and probably not here. This thread is about development. I thought it may be interesting to follow it from the beginning for “kids” so technically inclined and so much in loved with their cars. I know it would be for me.
#31
Originally Posted by Kennedy
Fair enough...
I have a Mech Eng. BE degree... so I know your language, but have never applied it outside my own wrenching and "pleasure reading"... It seems the USMC had other plans (IT/Comm) for this 20 lb head.
I have a Mech Eng. BE degree... so I know your language, but have never applied it outside my own wrenching and "pleasure reading"... It seems the USMC had other plans (IT/Comm) for this 20 lb head.
Although I diasagree about connecting rods and forces exerted, I can see what your trying to say... Although the fork itself predominantly deals with forces in the vertical, it also deals with a lot of torsional and lateral force (engine rock, hitting a hard bump while turning etc.), which is my view of the difference.
On the other hand, connecting roads are under tremendous lateral forces coming from inertia.
Certainly material selection, dynamic loads and cycling, hell even corrosion should all be considerations... Given the simplicity of the design, that's a prime candidate for a completely "overengineered" solution.
Good luck, I look forward to your progress.
From a more practical perspective,
Are you concerned about bottoming out? The stock suspension is a bit soft and underdamped to be riding that low... Perhaps some spring reenforcements should be included...?
Anyway, glad to hear you are where you are. There's nothing more dang
From a more practical perspective,
Are you concerned about bottoming out? The stock suspension is a bit soft and underdamped to be riding that low... Perhaps some spring reenforcements should be included...?
Anyway, glad to hear you are where you are. There's nothing more dang
#32
Ouch, that was bit unwarranted...
- My first post was not a rush to bash, but a valid design concern. Given your rather obscure posts, one could not be sure of your background, or the effort that went into this mod. My concerns we're predominanly around "disribution" without demonstartion of safety.
- Although I respectfully disagree with yuor assessment of the front suspension and the lateral/torsional forces applied, I am not articulate nor versed enough in the dynamic forces of double wishbone geometery to argue differently.
- "dangerous improvisation"... hmm. I reread my post, nowhere did I say or imply that. Finding the right measure? Sure, you have the tools for that? I was implying with "overengineering" that you could make this as beefy as you wanted for safety's sake with little to no reason "not to". Why don't you discuss what you've done to find the right measure? What equipment, data do you have to measure peak lateral load of the fork, stress points etc. I assume you have some modelling software that will spit out some form of part dimensions based on this data... meh.
- Do the lower arms have travel limiters? I've never really looked at this approach to a drop. Shortening the strut length achieves drop by rotating the lower arm up. That arm can only "stuff" so far up, before you'll need to worry about CV axle binding, brake line length (which is easiliy addressed), and I really think the limiting factor is bushing 10 as the arm pivots on that bushing.
Now... with that said, If I'm not mistaken, the A-spec uses progressively wound springs which would mean the most of the spring resistance is soft and squishy, until you reach the end of the struts compression, where the springs exponentially get stiffer. Since you've shortened the fork, I'm worried #10/CV would bind/bottom before the A-spec reached the stiffer part of the supension travel... and that would be bad.
Either way, you obviously have done more research and engineering than feeding "a little program into a CNC machine". Your first post left me with a much different impression as well.
Unfortunately, I doubt you're gonna get much more of a discussion from others, other than "gimme gimme". This place doesn't have many real engineers show up... which clearly you are the superior, and with an attitude of playing smackdown with those less expereinced, I doubt other will bother tangling with you.
Good luck in your efforts...
- My first post was not a rush to bash, but a valid design concern. Given your rather obscure posts, one could not be sure of your background, or the effort that went into this mod. My concerns we're predominanly around "disribution" without demonstartion of safety.
- Although I respectfully disagree with yuor assessment of the front suspension and the lateral/torsional forces applied, I am not articulate nor versed enough in the dynamic forces of double wishbone geometery to argue differently.
- "dangerous improvisation"... hmm. I reread my post, nowhere did I say or imply that. Finding the right measure? Sure, you have the tools for that? I was implying with "overengineering" that you could make this as beefy as you wanted for safety's sake with little to no reason "not to". Why don't you discuss what you've done to find the right measure? What equipment, data do you have to measure peak lateral load of the fork, stress points etc. I assume you have some modelling software that will spit out some form of part dimensions based on this data... meh.
- Do the lower arms have travel limiters? I've never really looked at this approach to a drop. Shortening the strut length achieves drop by rotating the lower arm up. That arm can only "stuff" so far up, before you'll need to worry about CV axle binding, brake line length (which is easiliy addressed), and I really think the limiting factor is bushing 10 as the arm pivots on that bushing.

Now... with that said, If I'm not mistaken, the A-spec uses progressively wound springs which would mean the most of the spring resistance is soft and squishy, until you reach the end of the struts compression, where the springs exponentially get stiffer. Since you've shortened the fork, I'm worried #10/CV would bind/bottom before the A-spec reached the stiffer part of the supension travel... and that would be bad.
Either way, you obviously have done more research and engineering than feeding "a little program into a CNC machine". Your first post left me with a much different impression as well.
Unfortunately, I doubt you're gonna get much more of a discussion from others, other than "gimme gimme". This place doesn't have many real engineers show up... which clearly you are the superior, and with an attitude of playing smackdown with those less expereinced, I doubt other will bother tangling with you.
Good luck in your efforts...
#33
I'm in the same boat with Kennedy. I do applaud your efforts and give you much deserved props, but with my engineering background, I need to see either a COSMOS or and ANSYS stress distribution chart. A couple of stability tests wouldn't hurt either.
Like Kennedy said, some folks will overlook safety and say "gimme gimme" if it will save them a couple hundred bucks to lower their car. Engineering is great because like you just proved, you can make a ton of cool things. However, there are tremendous consequences if proper liability issues aren't resolved first.
I'm not here to put you down or anything like that. Just chiming in as a fellow engineer and would definitely be interested once those issues are taken care of.
Like Kennedy said, some folks will overlook safety and say "gimme gimme" if it will save them a couple hundred bucks to lower their car. Engineering is great because like you just proved, you can make a ton of cool things. However, there are tremendous consequences if proper liability issues aren't resolved first.
I'm not here to put you down or anything like that. Just chiming in as a fellow engineer and would definitely be interested once those issues are taken care of.

#34
Originally Posted by Kennedy
Ouch, that was bit unwarranted...
- My first post was not a rush to bash, but a valid design concern. Given your rather obscure posts, one could not be sure of your background, or the effort that went into this mod. My concerns we're predominanly around "disribution" without demonstartion of safety.
- My first post was not a rush to bash, but a valid design concern. Given your rather obscure posts, one could not be sure of your background, or the effort that went into this mod. My concerns we're predominanly around "disribution" without demonstartion of safety.
What equipment, data do you have to measure peak lateral load of the fork, stress points etc. I assume you have some modelling software that will spit out some form of part dimensions based on this data... meh.
- Do the lower arms have travel limiters? I've never really looked at this approach to a drop. Shortening the strut length achieves drop by rotating the lower arm up. That arm can only "stuff" so far up, before you'll need to worry about CV axle binding, brake line length (which is easiliy addressed), and I really think the limiting factor is bushing 10 as the arm pivots on that bushing.
Now... with that said, If I'm not mistaken, the A-spec uses progressively wound springs which would mean the most of the spring resistance is soft and squishy, until you reach the end of the struts compression, where the springs exponentially get stiffer. Since you've shortened the fork, I'm worried #10/CV would bind/bottom before the A-spec reached the stiffer part of the supension travel... and that would be bad.
Either way, you obviously have done more research and engineering than feeding "a little program into a CNC machine". Your first post left me with a much different impression as well.
Unfortunately, I doubt you're gonna get much more of a discussion from others, other than "gimme gimme". This place doesn't have many real engineers show up... which clearly you are the superior, and with an attitude of playing smackdown with those less expereinced, I doubt other will bother tangling with you.
Good luck in your efforts...

#35
Originally Posted by Midnight_TL
I'm in the same boat with Kennedy. I do applaud your efforts and give you much deserved props, but with my engineering background, I need to see either a COSMOS or and ANSYS stress distribution chart. A couple of stability tests wouldn't hurt either.

However, there are tremendous consequences if proper liability issues aren't resolved first.

I'm not here to put you down or anything like that. Just chiming in as a fellow engineer and would definitely be interested once those issues are taken care of.


#36
I am not an engineer and don't know as much about suspensions like you brainiacs but my one question is; if it really is so easy to get a car lowered with a cheaper alternative like those forks, without drawbacks, how come company like Tein, Eibach, etc. dosen't sell these forks themselves? They could offer springs for the stiffer ride and lower looks and forks for the people who just want the looks? If it is a viable option it's hard to believe these huge suspension component companies would miss out making millions on it.
#37
Originally Posted by rockyfeller
I am not an engineer and don't know as much about suspensions like you brainiacs but my one question is; if it really is so easy to get a car lowered with a cheaper alternative like those forks, without drawbacks, how come company like Tein, Eibach, etc. dosen't sell these forks themselves? They could offer springs for the stiffer ride and lower looks and forks for the people who just want the looks? If it is a viable option it's hard to believe these huge suspension component companies would miss out making millions on it.
By the way, this concept is not just for looks. It keeps original suspension characteristics, which is best compromise in most cases, especially for sport sedans like TL A-spec or TL Type S. It improves handling by lowering center of gravity and increasing negative chamber angle without spoiling ride quality.
#38
Whatever aluminum you used (hopefully its a 7000 series, aircraft quality alloy, which was Type 3 anodized to limit oxidation) will have material properties that are markedly inferior to the steel part you replaced.
Duplicating the geometry of the steel part would therefore be an erroneous approach. The lower bolt thru-holes would be of particular concern.
The aluminum part would have to be completely redesigned (i.e. with thicker walls), but only after the mechanical limits of the existing part were established.
Duplicating the geometry of the steel part would therefore be an erroneous approach. The lower bolt thru-holes would be of particular concern.
The aluminum part would have to be completely redesigned (i.e. with thicker walls), but only after the mechanical limits of the existing part were established.
#39
http://www.matweb.com/search/Specifi...bassnum=M104BL
Those are the mechanical properties of 1040 carbon steel in a form that would be an excellent candidate for an OEM suspension component such as that front fork.
Note the tensile yield strength in particular.
You're not going to come anywhere close to that with the overwhelming majority of aluminums and even the strongest 7000 aluminum alloys can't touch it in terms of ultimate yield strength.
Using any type of CAST (vs. forged) aluminum will result in catastrophe.
I'd strongly caution against this mod unless you've re-engineered the part's geometry to accommodate the weaker material. I also agree that half-shaft contact/damage is of real concern here.
Those are the mechanical properties of 1040 carbon steel in a form that would be an excellent candidate for an OEM suspension component such as that front fork.
Note the tensile yield strength in particular.
You're not going to come anywhere close to that with the overwhelming majority of aluminums and even the strongest 7000 aluminum alloys can't touch it in terms of ultimate yield strength.
Using any type of CAST (vs. forged) aluminum will result in catastrophe.
I'd strongly caution against this mod unless you've re-engineered the part's geometry to accommodate the weaker material. I also agree that half-shaft contact/damage is of real concern here.
#40
Originally Posted by harddrivin1le
http://www.matweb.com/search/Specifi...bassnum=M104BL
Those are the mechanical properties of 1040 carbon steel in a form that would be an excellent candidate for an OEM suspension component such as that front fork.
Note the tensile yield strength in particular.
You're not going to come anywhere close to that with the overwhelming majority of aluminums and even the strongest 7000 aluminum alloys can't touch it in terms of ultimate yield strength.
Using any type of CAST (vs. forged) aluminum will result in catastrophe.
I'd strongly caution against this mod unless you've re-engineered the part's geometry to accommodate the weaker material. I also agree that half-shaft contact/damage is of real concern here.
Those are the mechanical properties of 1040 carbon steel in a form that would be an excellent candidate for an OEM suspension component such as that front fork.
Note the tensile yield strength in particular.
You're not going to come anywhere close to that with the overwhelming majority of aluminums and even the strongest 7000 aluminum alloys can't touch it in terms of ultimate yield strength.
Using any type of CAST (vs. forged) aluminum will result in catastrophe.
I'd strongly caution against this mod unless you've re-engineered the part's geometry to accommodate the weaker material. I also agree that half-shaft contact/damage is of real concern here.
I agree that contact between half-shaft and shock absorber would be bad. Not really disastrous, as some may think, but bad. Actually that is limiting factor so this concept can’t go lower than 1.5” at front.